55 Suggerimenti e best practice per il prelievo degli ordini da magazzino esperto
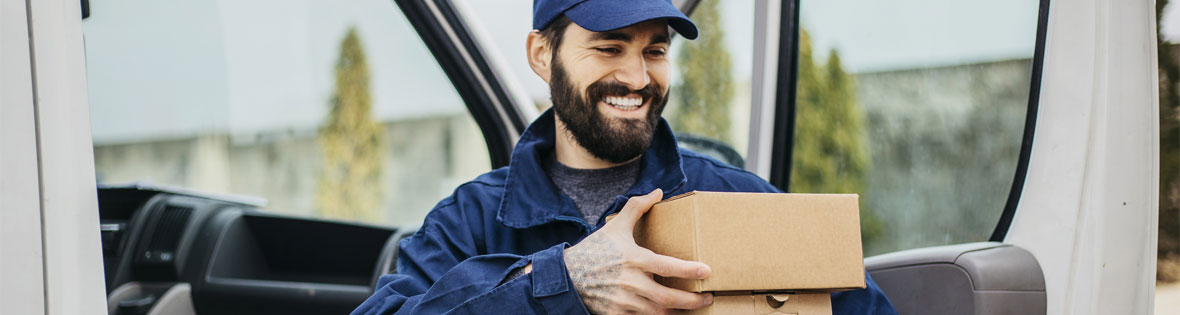
Ci sono molti processi in entrata e in uscita coinvolti nello spostamento e nella gestione dell'inventario che costituiscono la disciplina della gestione del magazzino. Le aziende spesso si concentrano sui processi in uscita per aumentare la soddisfazione dei clienti e ridurre le inefficienze ei costi operativi.
Ma il prelievo degli ordini è una parte cruciale della gestione del magazzino in uscita. Costituisce tutti i passaggi necessari per il recupero fisico degli articoli immagazzinati nel magazzino per evadere un ordine del cliente.
Importanza di migliorare la preparazione degli ordini in magazzino
Le aziende intelligenti cercano di migliorare il prelievo degli ordini per una buona ragione:è l'attività più laboriosa e costosa nel magazzino, in genere rappresentano più della metà dei costi operativi del magazzino.
I miglioramenti nella raccolta degli ordini aiutano le aziende a consegnare i prodotti giusti ai clienti più velocemente, e spendere meno soldi per i passaggi associati. I selezionatori degli ordini di magazzino in genere prendono una lista di prelievo e si spostano in diversi punti del magazzino per ottenere gli articoli, cercali sugli scaffali del magazzino, estrarli e abbinare i documenti per garantire l'accuratezza dell'ordine prima della spedizione.
La parte più dispendiosa in termini di tempo del processo di commissionamento è il viaggio, che occupa il 55% del tempo del selezionatore di magazzino, in media, seguito da pratiche burocratiche e altre attività (20%), ricerca (15%) ed estrazione (10%), secondo una ricerca del Georgia Tech Supply Chain and Logistics Institute. Per questa ragione, gran parte del lavoro per migliorare i processi di commissionamento è finalizzato alla riduzione dei tempi di viaggio improduttivi.
Per ottenere un picking degli ordini di prim'ordine è necessario sapere dove si trovano i prodotti, esattamente quanti sono disponibili, sapere quanti ne hai bisogno, in modo da non prelevare per ogni singolo ordine uno alla volta, e assicurarti che siano posizionati strategicamente per facilitare il prelievo e l'elaborazione rapida per la spedizione.
Quindi, come possono le aziende ridurre al minimo i tempi di preparazione degli ordini, garantendo al tempo stesso un'evasione accurata degli ordini e la sicurezza dei dipendenti in un magazzino?
55 Suggerimenti e best practice per il prelievo degli ordini in magazzino da adottare
Poiché non esiste un unico modo per garantire ordini perfetti, ci sono molti metodi, strumenti e processi che un'azienda può utilizzare per migliorare il prelievo degli ordini. La combinazione di strategie, le migliori pratiche e le tecnologie che la tua organizzazione dovrebbe adottare dipenderanno dal settore, numero di articoli venduti e velocità con cui l'inventario si muove attraverso i magazzini.
Osservare il design del magazzino e i metodi di prelievo degli ordini utilizzati all'interno delle sue quattro mura aiuterà un'azienda a selezionare i processi adeguati, tecnologie e attrezzature per migliorare il commissionamento.
Suggerimenti per la progettazione del magazzino per il prelievo degli ordini
L'eccellenza nella preparazione degli ordini inizia dalla scelta del design e del flusso di magazzino giusti per la strategia dei processi aziendali.
-
Scegli un tipo e un flusso di magazzino. I magazzini sono generalmente progettati per spostare le merci in uno dei layout seguenti (o in una combinazione di essi).
- Flusso a forma di U posiziona le banchine di ricezione e spedizione sullo stesso lato dell'edificio, e i prodotti si muovono a forma di U dalla ricezione alla spedizione. Questo design offre spazio di attracco condiviso ed è in genere il migliore per piccoli edifici.
- Flusso a forma di I metti la ricezione a un'estremità e la spedizione all'altra estremità dell'edificio in modo che tutte le merci si muovano in un'unica direzione. Un flusso a forma di I va bene per le aziende ad alto volume, così come quelli che necessitano di un forte controllo di sicurezza sulle merci in entrata e in uscita dal magazzino.
- Flusso di magazzino a forma di L ha lo scarico in entrata su un'estremità e la spedizione in uscita con un angolo perpendicolare a quell'area. Ciò può rendere più facile il cross-docking, quando gli articoli vengono prelevati da un camion e caricati immediatamente su un altro. Questo è un bene per le aziende che potrebbero non immagazzinare mai prodotti sugli scaffali, spedire le scorte subito dopo averlo portato in.
-
Decidi come il prodotto è organizzato all'interno di quel flusso. Questo potrebbe essere quello che viene chiamato un progetto di magazzino triadico, che è suddivisa in tre zone:in rapido movimento, prodotto medio e lento. Nei magazzini che non utilizzano questo design, il prodotto non è suddiviso in zone. Molti magazzini adottano un design in cui automatizzano una sezione con articoli adatti e hanno ancora persone coinvolte nel prelievo degli articoli, di qualche grado, nell'altro.
- Posiziona i prodotti che si muovono più velocemente più vicini all'evasione degli ordini in modo che siano facili da scegliere.
- Conserva gli articoli che spesso si vendono insieme uno vicino all'altro.
Metodi di prelievo degli ordini di magazzino
Se non disponi di un metodo di prelievo, preleverai per ogni ordine in ordine cronologico senza visibilità sugli altri ordini nella tua coda:questo porta a perdere molto tempo ad attraversare il magazzino per recuperare lo stesso articolo durante il giorno.
-
Le operazioni con un volume di ordini basso o che vendono prodotti di fascia alta o pesanti dovrebbero essere discreti, prelievo dell'ordine individuale, prelievo pezzo o picker-to-part. Questo è il metodo di commissionamento più semplice, in cui una persona preleva l'ordine completo, passeggiando per il magazzino, tirando tutti gli elementi necessari e spesso consolidandoli in un contenitore.
-
Per le organizzazioni che devono prelevare e imballare rapidamente ordini di più articoli e hanno un numero elevato di SKU e prelievi per ordine, il wave picking è una buona scelta. Il prelievo viene effettuato a ondate programmate, e tutte le zone vengono selezionate contemporaneamente. Gli articoli vengono ordinati a valle man mano che vengono preparati per le singole spedizioni. I posti di prelievo dell'onda come ordini insieme in base a regole predefinite e li rilascia per essere evasi insieme in modo che i prelievi possano prelevare per l'intera ondata contemporaneamente.
-
Per aumentare l'efficienza di prelievo, i lavoratori possono prelevare in lotti in cui prelevano per più ordini, ad esempio articoli simili o articoli situati in aree simili, in un unico viaggio. Per le aziende con un basso numero di prelievi per ordine, la raccolta in batch può ridurre i tempi di viaggio. L'operatore entra nel magazzino, preleva l'intera quantità di articoli richiesta e poi li assegna a ogni singolo ordine.
-
Per grandi magazzini con molti SKU, la scelta della zona è spesso vantaggiosa. Il prelievo a lotti può incorporare il metodo di prelievo a zona, in cui un selezionatore ha il compito di curare una determinata area del magazzino, ottenere tutti gli articoli per la loro zona e quindi passare l'ordine. Per questa ragione, il prelievo a zona è anche noto come pick and pass. Gli oggetti possono muoversi, ad esempio, lungo un nastro trasportatore fino a quando tutti gli articoli necessari non sono nella scatola.
-
Le aziende innovative stanno provando configurazioni e sistemi di smistamento efficaci per aumentare l'efficienza del processo di prelievo. Il selettore di magazzino rimane in un posto, e i prodotti vengono portati al selezionatore da un trasportatore, un dispositivo robotico o qualche altra tecnologia automatizzata. Pensa alla buona persona come all'automazione del processo di prelievo discreto.
-
Un altro modo per ridurre i tempi di viaggio è il pick-to-box. Pick-to-box integra una maggiore automazione nel prelievo batch. Le aree di prelievo possono essere organizzate in stazioni di prelievo, ciascuno collegato da un nastro trasportatore. Il selezionatore riempie la scatola con i prodotti di cui è responsabile e sposta la scatola fino all'evasione dell'ordine.
Attrezzature e tecnologia per la preparazione degli ordini in magazzino
Un altro aspetto chiave della gestione del magazzino è la tecnologia che supporta la strategia ottimale per la struttura e la natura dell'attività. Ad esempio, un'azienda con un basso numero di SKU e un minor numero di linee selezionate può utilizzare un metodo di prelievo dell'ordine individuale, e sfrutta la tecnologia pick-to-belt o pick from pallet. Le aziende con un gran numero di SKU che movimentano volumi elevati possono optare per il prelievo in batch e la tecnologia vocale o pick-to-light.
Nel considerare quali attrezzature e tecnologie sono adatte al tuo magazzino:
-
Allinea la tecnologia al numero di SKU e al volume. Guarda il numero di righe in elaborazione al giorno rispetto al numero di prodotti. Generalmente, maggiore è il numero di SKU e il numero di righe, maggiore è la necessità di automazione.
-
Inizia implementando un sistema di gestione del magazzino (WMS). Anche le operazioni di magazzino più semplici richiedono una qualche forma di sistema di gestione del magazzino. Cerca la funzionalità di base di prelievo degli ordini per archiviare e tenere traccia degli SKU e della posizione degli articoli e automatizzare la creazione di elenchi di prelievo dagli ordini dei clienti. Un WMS controllerà un ordine del cliente rispetto all'inventario disponibile e fornirà istruzioni sotto forma di elenco di prelievo. Tiene conto della disposizione del magazzino, manodopera disponibile e l'ubicazione delle attrezzature per massimizzare l'efficienza e garantire l'accuratezza nel prelievo degli ordini.
-
Integra una qualche forma di tecnologia di prelievo mobile. Dagli scanner RF mobili di base, alle tecnologie che dirigono i prelievi illuminando i pulsanti sugli scaffali in un percorso di prelievo (pick-to-light) o guidano a voce un selezionatore dotato di cuffie (pick-to-voice), ci sono molte tecnologie mobili che sono essenziali per un accurato prelievo degli ordini, guidando gli utenti nel corridoio esatto, lo scaffale, o bin nel percorso più logico. Assicurati che le tecnologie utilizzate sul pavimento possano comunicare facilmente con il WMS in modo da non introdurre inutili complessità.
-
Assicurati che il WMS sia integrato con il sistema ERP. Il monitoraggio dei movimenti e delle merci nel magazzino fornisce una grande quantità di dati preziosi per altri reparti, come l'acquisto o il servizio clienti. Assicurati che queste altre funzioni abbiano accesso agli stessi dati all'interno del software che usano per il loro lavoro.
-
Seleziona il giusto sistema di movimentazione dei materiali e regola i sistemi man mano che gli SKU e il volume aumentano. Un aumento del numero di SKU richiede molta più logistica nel magazzino. Con SKU bassi e volume ridotto, un semplice sistema di movimentazione dei materiali come può fare un carrello elevatore, ma con l'aumentare del volume e della complessità, l'azienda avrà bisogno di più meccanizzazione. Le attrezzature per la movimentazione dei materiali sono uno spazio innovativo che sfrutta molte idee e tecnologie innovative.
-
Prendere in considerazione i progressi nelle attrezzature per consentire la configurazione del corridoio stretto. L'ottimizzazione dello spazio disponibile nel magazzino offre vantaggi oltre allo stoccaggio:può anche aiutare a ridurre i tempi di viaggio nel processo di prelievo degli ordini. I corridoi di magazzino convenzionali sono larghi 12-14 piedi. I corridoi stretti sono in genere 8-10 piedi, ma può essere fino a sei piedi. Combinando le giuste tecnologie e attrezzature, i magazzini possono ottenere guadagni nel prelievo degli ordini con corsie più strette.
-
Massimizza lo spazio di magazzino utilizzando l'attrezzatura giusta. La tecnologia dei carrelli elevatori è in costante miglioramento, e ci sono camion in grado di attraversare corridoi stretti e in spazi ristretti, come il muletto articolato. Amazon sfrutta robot che assomigliano agli aspirapolvere Roomba. Questi robot trasportano gli articoli necessari dagli scaffali al raccoglitore e li spingono indietro in spazi ristretti quando tutti gli articoli vengono recuperati.
-
Implementa la tecnologia del trasportatore. Esistono dozzine di tipi di tecnologia di trasporto che possono essere utilizzati per un prelievo più efficiente, così come la salute ergonomica dei dipendenti che svolgono il lavoro.
-
Guarda i progressi nelle tecnologie di smistamento. In combinazione con trasportatori, le tecnologie di smistamento forniscono un aumento della precisione e dell'efficienza, producendo tempi di consegna più brevi e maggiore accuratezza.
-
Scopri qual è lo storage giusto per l'azienda e non trascurare i vantaggi delle tecnologie automatizzate. una giostra, ad esempio, automatizza il picking tramite una scaffalatura che ruota lungo un binario per portare gli articoli al picker. Possono essere configurati in base al metodo di prelievo scelto dall'azienda.
-
Comprendi tutte le opzioni disponibili per la tecnologia di prelievo automatizzato. Alcune aziende hanno molto successo con le apparecchiature pick-to-light o pick-to-voice. Con pick-to-light, i raccoglitori scansionano il codice a barre di un ordine e la quantità e la posizione dell'articolo si illuminano. Pick-to-voice guida il selezionatore e fornisce conferma tramite un auricolare. Oggi, le tecnologie di realtà aumentata stanno consentendo progressi come gli occhiali pick-via-smart, che visualizzano digitalmente la posizione e la quantità di un articolo tramite un auricolare indossabile. Forniscono istruzioni guidate dalla voce e la possibilità di eseguire scansioni direttamente con l'auricolare, consentendo all'operatore di utilizzare entrambe le mani e massimizzare l'efficienza con meno tocchi.
-
Implementa tecnologie intelligenti. Le tecnologie IoT possono aiutare a fornire conteggi di inventario in tempo reale, mentre l'avanzare della tecnologia dei dispositivi indossabili come gli occhiali intelligenti sta rendendo più facile tenere traccia del movimento dell'inventario e garantire che il conteggio giusto sia lì per cominciare. Ciò consente di risparmiare tempo al raccoglitore e la frustrazione di cercare oggetti che non ci sono.
-
Esplora il potenziale dei robot raccoglitori. I robot raccoglitori possono effettivamente fare la raccolta, con la possibilità di raggiungere scaffali alti e recuperare oggetti da imballare, mentre sono anche dotati di sensori che impediscono loro di urtare persone o scaffali.
-
Conosci i co-bot. I co-bot possono essere utili da distribuire per attività che hanno qualche ripetizione, ma richiedono anche un certo livello di intervento umano. Il co-bot può mettere insieme la scatola, Per esempio, o recupera oggetti con forma o peso prevedibili, come una scatola da scarpe.
Best practice e strategie di prelievo degli ordini dal magazzino
Il design del magazzino, I metodi e le tecnologie di prelievo degli ordini ti aiuteranno a determinare quale delle seguenti strategie ha più senso implementare per migliorare i tuoi processi di prelievo degli ordini.
Inizia con un obiettivo chiaro su cosa vuoi migliorare e come lo misurerai, quindi seleziona i suggerimenti che hanno più senso.
-
Chiedi alle persone che lavorano nel magazzino dove sono i colli di bottiglia. Non dimenticare le tante persone che spesso supportano i tuoi processi, compresi gli amministratori degli uffici, operatori di apparecchiature e altri.
-
Non basare gli obiettivi di prelievo degli ordini su medie. La stagionalità e le tendenze economiche influenzeranno notevolmente il modo in cui le scorte entrano ed escono dal magazzino. Guarda i picchi e gli avvallamenti, applicare statistiche e utilizzare algoritmi per determinare obiettivi ragionevoli.
-
Tieni traccia della produttività del raccoglitore. Conoscere i livelli di produttività consente al responsabile del magazzino di progettare i turni in base a come suddividere al meglio il lavoro. Guarda le scelte medie per persona-ora, così come l'inverso, ore-persona medie per prelievo. Il lavoro medio per ordine è quindi il numero medio di righe di prelievo per ordine moltiplicato per le ore-persona medie per prelievo.
-
Misura e migliora il tempo totale del ciclo dell'ordine o il tempo del ciclo interno dell'ordine. Il prelievo degli ordini è una parte importante del calcolo del tempo totale necessario per elaborare un ordine. Il monitoraggio di questo numero fornisce una misura dell'efficienza di prelievo.
-
Esaminare l'accuratezza del conteggio dell'inventario in base alla posizione e gli errori relativi alla posizione di prelievo (come esaurimento scorte/ordini arretrati). Questo indica che non c'è una quantità sufficiente nella posizione designata.
-
Misura il tasso di riempimento (per riga e ordini) per confrontare gli articoli spediti quel giorno con il totale degli articoli ordinati quel giorno. Il tasso di riempimento è un buon modo per assicurarsi che le operazioni di magazzino soddisfino la domanda dei clienti e in genere viene calcolato giornalmente.
-
Misurare la precisione del prelievo degli ordini. L'accuratezza del prelievo degli ordini è al terzo posto tra i benchmark più importanti per i magazzini nel rapporto di benchmarking DC Measures del 2020. Una bassa precisione nel prelievo degli ordini indica la necessità di processi più efficienti, migliori standard di controllo, formazione più approfondita e altro ancora.
-
Non dimenticare i KPI che misurano la produttività dei dipendenti. Questi includono le linee spedite prelevate all'ora, linee spedite per ore dirette, linee spedite per totale ore del centro di distribuzione (DC), ore DC totali annue/costo DC totale e costo DC per lavoro totale utilizzato.
-
Seleziona non più di sei benchmark, metriche mirate che aiuteranno a gestire il magazzino in modo più efficiente e confrontare l'efficienza di più strutture.
-
Rivedi lo spazio del tuo magazzino ogni volta che conduci il tuo conteggio fisico. Un magazzino di beni di consumo in rapido movimento dovrà essere aggiornato almeno ogni cinque anni, mentre le gamme di prodotti, gli appetiti dei consumatori e le maggiori forze economiche cambiano. La mancata evoluzione del design del magazzino ostacolerà le strategie e i miglioramenti di prelievo degli ordini.
-
Esercitati a contare i cicli per eliminare la complessità e gli sprechi di SKU.
-
Tecniche come l'analisi dell'inventario ABC (di cui esistono diversi tipi) consentono alle aziende di classificare e organizzare gli SKU e rimuovere o spostare prodotti che intasano le loro operazioni.
-
Guarda oltre la classifica delle SKU solo per volume di dollari, ma anche come ogni SKU consuma risorse come lavoro e spazio. Classifica gli SKU in base al numero di volte in cui sono stati selezionati durante un determinato intervallo, redditività, o difficoltà di fabbricazione, Per esempio.
-
Implementa alcuni principi snelli. Conduci regolari passeggiate di Gemba, trascorrendo del tempo a osservare i processi di magazzino e a capire davvero come vengono completati, per identificare le inefficienze nella struttura. Le aziende possono anche implementare tecniche di poka-yolk, dove mettono a prova di errore le loro operazioni e cercano modi per evitare errori involontari. Un esempio qui sta guardando come il cross-dock può migliorare il flusso nel magazzino.
Suggerimenti per il prelievo degli ordini in magazzino
Una volta che il personale del magazzino sa dove l'azienda concentrerà i suoi sforzi, può iniziare a implementare i suggerimenti di seguito per aumentare l'efficienza e la precisione e migliorare la sicurezza dei lavoratori.
-
Conserva insieme gli SKU più diffusi. La densità di prelievo può essere aumentata, almeno a livello locale, memorizzando insieme gli SKU più popolari. Quindi, i commissionatori possono effettuare più prelievi in una piccola area, riducendo la quantità di spazio che devono coprire e aumentando la produttività.
-
Prestare molta attenzione allo slot del prodotto. Lo slotting si riferisce al posizionamento accurato delle singole casse all'interno del magazzino, in modo tale che tipi simili di inventario vengano immagazzinati insieme. Possono essere raggruppati per dimensione fisica, articoli spesso ordinati insieme, stagionalità e non solo. Inserendo correttamente il prodotto, le organizzazioni possono ottenere fino al 30% di risparmio di manodopera e garantire anche una migliore ergonomia nel magazzino, Segreti della catena di approvvigionamento dice. Slot in base al volume e al movimento e rivisita la strategia una o due volte l'anno. Un WMS può aiutare a identificare strategie di slotting adeguate e ci sono molti algoritmi che possono aiutare qui.
-
Ordini batch a riga singola. Gli ordini a riga singola sono ordini cliente per un solo articolo. Per questa ragione, non richiederanno l'ordinamento alla fine di un percorso di prelievo e puoi aumentare l'efficienza facendo in modo che un selezionatore ne ottenga il maggior numero possibile in un solo viaggio.
-
Rifornimento e prelievo del saldo per garantire che gli articoli siano presenti. Supply Chain Secrets dice che una regola pratica è un rifornitore ogni cinque raccoglitori, ma che dipende dai particolari modelli di flusso. Qualche volta, i magazzini commettono l'errore di misurare i prodotti solo in base al fatturato, quando dovrebbero guardare il movimento del prodotto, factoring in volume e vendite.
-
Assicurati che i documenti giusti siano associati all'ordine giusto. Un quinto del tempo di un selezionatore di magazzino va ad assicurarsi che i documenti siano corretti, per Georgia Tech. Questo può essere notevolmente facilitato implementando scanner RF, che automatizzano il processo e garantiscono la precisione stampando la distinta di imballaggio per l'ordine.
-
Liste di prelievo strutturate per un imballaggio efficiente. Pensa a come gli articoli si adatteranno meglio alla scatola in cui verranno spediti. Un WMS può sequenziare i prelievi in una lista di prelievo in modo che gli articoli di grandi dimensioni vengano prelevati per primi, Per esempio.
-
Massimizza la densità dei colpi. Un modo per farlo è aumentare la densità dei plettri, riducendo al minimo la distanza tra i prelievi per aumentare il numero di prelievi per punto e, di conseguenza, aumentare la produttività.
-
Non mischiare più SKU nelle stesse ubicazioni. Molti magazzini hanno ancora un'ubicazione legata solo a un livello di scaffale contenente fino a dieci SKU differenti. Ciò richiede che il dipendente cerchi in più prodotti l'articolo corretto.
-
Cerca di ridurre al minimo i tocchi della merce. Nella maggior parte dei magazzini, da sette a otto persone dall'ingresso all'uscita fino alla gestione del magazzino toccano un articolo, ma le aziende best-in-class avranno solo tre o quattro tocchi. Un modo per ridurre al minimo i tocchi è che i selezionatori raccolgano gli articoli e li inseriscano direttamente nella scatola di spedizione, non bidoni di plastica su un carrello.
-
Integra le misurazioni del peso con WMS. Le aziende che spediscono articoli grandi e pesanti possono aumentare la precisione del prelievo degli ordini collegando le informazioni sul peso dell'articolo all'elenco di prelievo. Se la scelta è, ad esempio, un'unità in meno, il sistema avviserà automaticamente il lavoratore che il peso è troppo basso e gli chiederà di aggiungere un'altra unità.
-
Scegli dalla pila del pavimento. Una strategia di slotting del prodotto consiste nel consentire ai selezionatori di prelevare articoli ad alta rotazione da cartoni su pallet sul pavimento utilizzando un transpallet o un transpallet. Questo può essere più efficiente rispetto al tenere questi articoli a vendita rapida su scaffali per pallet alti.
-
Le persone dovrebbero scegliere utilizzando giostre orizzontali invece di ascensori verticali. Numerosi sforzi di benchmarking nel corso degli anni hanno dimostrato che costa di più scegliere verticalmente che orizzontalmente. Ma l'utilizzo della capacità del magazzino richiede che le cose siano anche immagazzinate verticalmente. Fai prelevare gli articoli a velocità più lenta dal magazzino verticale e mantieni gli articoli ad alta velocità a livello del pavimento.
-
Scegli da un'area di avanzamento o di prelievo rapido. Le aziende stanno progettando aree del loro magazzino per ospitare SKU popolari che si trovano al piano terra e vengono rifornite da scorte provenienti da altre aree del DC. Georgia Tech afferma che l'area di prelievo in avanti più comune è lo scaffale portapallet al piano terra che viene rifornito spostando i pallet verso il basso dai livelli più alti. Altri esempi sono uno scaffale di flusso di cartone rifornito dallo stoccaggio alla rinfusa, o attrezzature specializzate come un carosello o un telaio ad A che viene immagazzinato da qualche altra parte.
L'adozione di misure per formare e prendersi cura delle persone che lavorano nel magazzino è un'altra parte fondamentale per garantire efficienza, prelievo degli ordini accurato ed economico.
-
Assicurati che il ragionamento alla base della strategia di gestione del magazzino e il motivo per cui è importante per l'azienda sia compreso da tutto il personale del magazzino, non solo manager. Un ottimo esempio del perché questo è importante viene da SI Systems, che sottolinea che quando molte aziende implementano la verifica del doppio codice a barre, dove l'operatore scansiona la SKU del prodotto e poi il pallet, per migliorare la precisione. Però, l'operatore spesso esegue invece una doppia scansione del pallet perché è più veloce. Il dipendente lo fa perché desidera soddisfare i livelli di produttività o produttività e non si rende conto del motivo per cui la scansione di entrambi è fondamentale per l'accuratezza dell'inventario. Dovresti condurre un processo di formazione formale con i membri del team e spiegare la giustificazione aziendale per ogni parte di un processo.
-
Utilizza metriche reali per stabilire standard di prestazione realistici per i magazzinieri. Utilizza metriche come le righe d'ordine raccolte all'ora e il costo di prelievo per ogni riga d'ordine e cerca di migliorarle fornendo ai selezionatori le giuste tecnologie che faciliteranno una maggiore efficienza e precisione, come pick-to-light e pick-to-voice.
-
Favorire la cooperazione. Un dashboard o un centro di controllo di qualità può aiutare a monitorare le prestazioni complessive del magazzino per premiare e incoraggiare i team, ma cerca anche di evidenziare i guadagni dei singoli dipendenti. Visualizza le statistiche dei risultati migliori e incentiva una forte produttività e prestazioni di sicurezza.
-
Lavorare per ridurre gli straordinari. Confronta le ore complessive con l'output e guarda le righe d'ordine raccolte per ora di lavoro, ad esempio, per misurare l'efficienza del lavoro. Fattore di ore normali di lavoro rispetto a ore di straordinario, linee prelevate al giorno e numero di cartoni, cadauno o pallet prelevati per periodo. Confronta questo periodo nel periodo. Se questi numeri sono bassi, ma gli straordinari sono alti, scopri perché.
-
Adottare misure per rendere il luogo di lavoro più sicuro e conforme agli standard OSHA. Le migliori operazioni di magazzino hanno programmi formali di formazione sulla sicurezza e formazione continua. Mettere i prodotti nella cosiddetta “zona d'oro” per garantire una corretta salute ergonomica. Contrassegnare chiaramente i corridoi e le aree di lavoro con indicatori di sicurezza e mantenerli liberi da detriti e pericoli. Assicurarsi che tutti i DPI appropriati siano sempre indossati dagli addetti al magazzino, compresi gli elmetti, occhiali, guanti, maschere, uniformi adeguate e altro ancora.
-
Rivedere e perfezionare i processi regolarmente. Man mano che le strategie di prodotto cambiano, assicurati che lo faccia anche la strategia di magazzino. Le sfide della catena di approvvigionamento e gli sforzi per aumentare la resilienza della catena di approvvigionamento metteranno alla prova molti dei principi della gestione dell'inventario just-in-time che hanno guidato le operazioni di magazzino per anni. In molti casi, sarà necessario più spazio e le scorte potrebbero essere conservate per periodi di tempo più lunghi per essere pronte a sovraccarichi e carenze. Infatti, la domanda di spazio di magazzino è elevata — Il Wall Street Journal ha riferito che l'attività immobiliare industriale è aumentata del 43% da aprile a maggio 2020, con una domanda di magazzini superiore a 100, 000 piedi quadrati sono i più forti.
Ottimizza il prelievo degli ordini con il software di gestione del magazzino
Pensa all'ordine del cliente come a una lista della spesa che il raccoglitore deve soddisfare, con ogni voce della lista (nota come righe d'ordine) annotando l'articolo e la quantità. Idealmente, è in atto un sistema di gestione del magazzino per controllare l'inventario disponibile e dove trovarlo, oltre a riorganizzare gli ordini in una lista di prelievo che tiene conto del layout del magazzino per aumentare la velocità. Il numero di righe di prelievo può essere un'indicazione di quanto il lavoratore dovrà percorrere il magazzino per ottenere gli articoli necessari per gli ordini.
Le aziende possono rivolgersi ai sistemi di gestione del magazzino (WMS) per aiutare a gestire i processi in entrata e in uscita dei propri magazzini e ottenere visibilità su tutti gli SKU stoccati e sulla loro posizione. La funzionalità WMS si basa su quella di una soluzione di gestione dell'inventario, e ha anche capacità per aiutare con la strategia di archiviazione e la gestione della forza lavoro. Il WMS fornisce dettagli su tutti gli articoli nel magazzino:dimensioni fisiche, come è imballato, dove è memorizzato e il percorso più efficiente per raggiungerli.
Un WMS supporta la pianificazione degli appuntamenti, ricevere, garanzia di qualità, mettere via, monitoraggio della posizione, gestione degli ordini di lavoro, raccolta, imballaggio e consolidamento e spedizione. Il WMS trasforma un ordine cliente in un elenco di prelievo e tiene traccia dell'assemblaggio dell'ordine. Il WMS può gestire anche i processi inbound in un magazzino, che mostra dove deve essere immagazzinato l'inventario, monitoraggio della produttività dei lavoratori, garantire che gli ordini rispettino i programmi di spedizione e altro ancora. Può inoltre connettersi ai sistemi di gestione degli ordini e ERP. Nello specifico, per la funzione di prelievo, un robusto WMS può supportare pick-to-light, Operazioni dirette a radiofrequenza, pianificazione del lavoro, Slotting SKU e molto altro.
Il giusto WMS si ridimensionerà in base alla necessità di nuove funzionalità e si adatterà al cambiamento dei processi. Mentre l'edificio stesso può rimanere statico, i processi e le tecnologie di un'azienda non dovrebbero essere scolpiti nella pietra. Osservando costantemente i sistemi e il modo in cui le persone li utilizzano per svolgere il proprio lavoro, la gestione del magazzino può essere costantemente migliorata, aiutare i dipendenti a svolgere il proprio lavoro in modo più efficace e assicurarsi che i clienti continuino ad acquistare e a fidarsi della tua attività.
Attività commerciale
- 35 Metriche di e-commerce con formule, Benchmark e suggerimenti
- 51 Suggerimenti per la gestione del magazzino per la tua attività
- Guida definitiva al prelievo degli ordini:tipi, Metodi e suggerimenti
- Previsione dell'inventario:tipi,
- Inventario fisico:passaggi,
- Gestione dell'inventario al dettaglio:che cos'è,
- Spiegazione dell'automazione del magazzino:tipi,
- I migliori consigli, Trucchi, e strumenti per lavorare a distanza
- 11 migliori piani pensionistici:pro e contro
- Quando comprare un'azione e quando vendere un'azione:5 consigli
-
I migliori consigli e informazioni utili su come fare trading di criptovaluta
Prima di tuffarti a capofitto nel trading di Bitcoin, ci sono numerosi suggerimenti essenziali di cui hai bisogno se prevedi una corsa quasi fluida nella tua nuova impresa. Questa non è una promessa c...
-
È rischioso scambiare Altcoin? – Buone pratiche e informazioni utili
In larga misura, questa attuale pandemia ha devastato molte imprese e settori finanziari, compreso il mercato delle criptovalute. Sebbene Bitcoin abbia dominato il mercato delle criptovalute e registr...